包组编号:001
预算金额(元):71000000
最高限价(元):71000000
采购需求:查看
技术要求
一、概述
1.1 试验平台功能
本试验平台建成后将可进行燃气轮机型号测试工作,可开展全温全压条件下燃烧室燃烧实验和点熄火性能试验、喷嘴雾化试验、导叶冷效试验、旋转叶片冷效半物理仿真试验和涡轮轮缘封严试验等。
1.2 试验平台系统组成
本项目主要包含9个分系统:燃烧系统(燃烧-涡轮一体化)、喷雾实验系统、半物理仿真实验系统、3D打印、试车台控制系统、后处理系统、排放测试系统、气源系统和天然气系统。
1.3 系统布局
本项目为重大设备更新项目,建设地点拟定为沈阳航空航天大学,沈阳市道义经济开发区道义南大街37号。
气源为暂冲气源,由高压压气机组、高压气罐组以及高压管道系统等组成,高压气罐放置在能源与环境学院重点试验楼中楼东北角,原6台气罐放置位置。
除空气高压气罐和天然气瓶组外,其余系统全部放置在能源与环境学院重点试验楼东楼(C座)实验楼一层,平面布局如下图所示,红色框内为新增试验设施。
图1 重点试验楼东楼(C楼)平面布置图(红色线框内)
燃烧系统(燃烧涡轮一体化)、喷雾实验系统和半物理仿真实验系统在不同时进行试验,可以共用部分进气系统、冷却水系统、排气消音器、数采系统和电气控制系统等。具体设备布局和系统共用情况由投标人根据经验进行综合设计和优化。
二、技术指标
2.1 燃烧实验系统
2.1.1 燃烧实验系统总体技术指标参数(燃烧-涡轮一体化,含导轨基底建设和调台试验件设计)
★1) 空气进口流量5kg/s,进口压力3MPa,空气进口温度800K,燃气出口最高温度不低于1800K;
★2) 次流流量1kg/s,压力3MPa,次流温度:常温~473K;
★3) 燃油总流量150g/s,供油压力8MPa,流量控制精度±1%FS,流量测量精度±0.5%FS;
★ 4)须满足燃烧-涡轮(导叶冷效研究)一体化试验测试需求,其中燃烧试验段与涡轮测试段须相互独立,仅在开展导叶冷效研究时,将涡轮冷效测试段与燃烧排气段相替换;
▲5) 燃烧试验段出口须满足平板发汗冷却试验段的测试需求,其中燃烧试验段与发汗冷却试验段须相互独立,仅在开展发汗冷却研究时,将平板发汗冷却测试段与燃烧排气段相替换;
6) ★ 燃烧系统工位总长不小于20m,宽度不小于1.5m,燃烧系统及喷雾实验系统单侧至少预留2m的空间,以满足光学测量仪器对空间的使用要求。
2.1.2 燃烧实验系统工位系统详细技术指标参数(燃烧-涡轮一体化)
1) 燃烧系统主要由进气系统、排气系统、燃油系统、冷却水系统等组成,燃烧系统按高温高压设计,基于此燃烧系统开展高温高压多燃料低排放扩散燃烧试验、高温高压高效清洁燃烧技术试验、高温高压混合气预混燃烧试验、高温高压多燃料燃烧不稳定性试验和点熄火试验等。除此之外,在此基础上可开展涡轮导叶冷效试验、发汗冷却试验、火焰筒传热冷却试验、喷嘴热防护试验、火焰筒热态雾化试验和单头部筛选试验中的热态试验等。
表1 试验工位系统组成表
序号 | 子系统名称 | 单位 | 数量 |
1 | 燃烧系统工位进气系统 | 套 | 1 |
2 | 燃烧系统工位排气系统 | 套 | 1 |
3 | 燃烧系统工位燃油系统 | 套 | 1 |
4 | 燃烧系统工位燃料调节系统 | 套 | 1 |
5 | 燃烧系统工位冷却水系统 | 套 | 1 |
▲2) 气源系统采用暂充式气源,高压气存储在高压气罐内,分为两条供气流路,其中的主流路提供高压气源,为燃烧室提供高温高压环境,二次流路为试验段的燃烧室筒壁和涡轮叶片的冷效测试提供气流。加温器出口加整流孔板或稳定段,以产生均匀的燃烧室进口气流。
★3) 燃料调节系统包含液态燃料和气态燃料两条流路,液态燃料流路主要供给航空燃油,气态燃料主要供给天然气。
4) 冷却水系统主要针对试验测试段出口燃气的冷却,循环冷却水由流经水冷套管冷却水和喷淋段冷却水两部分组成。其中套管冷却水主要引自冷却水站,压力为1MPa;喷淋冷却水压力为4MPa。
★5) 须含导轨基底建设,并须对现有建筑场地地面和周围结构进行核算,确保基础能够承受设备所产生的载荷。
★6) 须满足如下考核详细工况参数表。
表2 燃烧系统工位试验参数需求表
序号 | 进气温度(K) | 进气压力(MPa) | 进气流量(kg/s) | 供油温度(K) | 供油压力(MPa) | 供油流量(g/s) | 备注 |
1 | 800 | 3 | 5 | 288~430 | 8 | 150 | |
2 | 700 | 2 | 3.5 | 288~430 | 8 | 100 | |
3 | 600 | 1.5 | 2 | 288~430 | 8 | 80 | |
4 | 550 | 1 | 1 | 288~430 | 8 | 40 | |
5 | 500 | 0.5 | 0.5 | 288~430 | 8 | 20 |
2.1.2.1 燃烧系统工位进气系统
1) 概述
进气系统用于为试验件提供一定压力和流量的空气,主要由管道、阀门、流量测量装置、整流器(若有)、测量仪器仪表和管道支架等组成。
试验器进气系统依次由总进气路、主进气路及次流进气路组成。
总进气路用于连接公用工程进气,总进气路主要由管道、开关阀和气滤等组成。
进气调节路用于调节进气系统出口空气压力和流量参数,主要由管道、开关阀、调节阀、流量测量装置和管道支架等组成。
进气路上设置有加温器,用于常温空气的加热。
次流进气路用于涡轮叶片气膜冷却供气、火焰筒传热冷却试验冷侧供气,主要由管道、开关阀、调节阀、流量测量装置和管道支架等组成。
2)进气系统需满足的功能要求
①进气系统空气流量、温度和压力应能满足试验参数需求;
▲②进气系统空气流量、温度和压力应能远程控制,并在整个试验参数需求范围内能够连续、灵活调节;
③在满足试验需求情况下,进气系统压损应尽量小;在满足试验需求前提下,进气系统温损应尽量小;
★④进气系统应具备良好的密封性,确保在任何情况下不得产生泄露;
3)总技术指标
①试验件进口(主流):
最高空气温度:800K;最高空气压力:3MPa;最大空气流量:5kg/s。
②试验件进口(次流):
空气温度:常温~473K;最高空气压力:3MPa;最大空气流量:1kg/s。
4)关键设备指标
① 阀门
阀门主要为开关阀和调节阀两大类。开关阀用于对管道介质进行通断控制,调节阀用于对介质流量或压力进行调节。阀门应满足以下要求:
a) 开关阀泄漏等级不低V级;
b) 调节阀泄漏等级不低于Ⅳ级,调节系统的调节精度优于1%;
c) 调节型阀门应具备阀位反馈功能,远程控制;
d) 阀门主体材质:不低于304不锈钢。
② 流量计
空气质量流量测量可采用标准喷嘴、孔板或文丘里管,其设计、制造和安装应符合本文件所提出的相关标准和规范。
a) 流量测量装置差压变送器精度优于0.25%;
b) 流量测量精度优于1%;
c) 主体材质:不低于304不锈钢。
③ 补偿器
采用波纹管补偿器补偿空气管道系统热位移时,设计和制造应按国标GB/T12777-1999《金属波纹管补偿器通用技术条件》进行,补偿器应具有良好的安全性、可靠性。补偿器需满足如下要求:
a) 设计疲劳寿命:≮1000次;
b) 实际使用寿命:≮5000小时。
2.1.2.2 燃烧系统工位排气系统
1) 概述
排气系统用于将燃烧室排出的高温燃气降温减速后引至排气消音器后放空,并根据试验工况的需要与进气系统匹配来调节燃烧室试验件进口压力。
主流排气系统管道主要由管道、喷淋段、背压阀、弯管、排气油气分离处理装置和管道支架等组成。
次流排气管道主要由管道、背压阀和管道支架等组成。
排气管道均排入消音器内,消音器内安装消音元件,使排气噪音满足要求。
2) 排气系统需满足的功能要求
① 排气系统应能与进气系统匹配满足试验参数范围及调节精度要求;
② 排气系统可承受试验件排气造成的压力与热负荷;
▲③ 排气管道设计时应避免喷淋水倒流或喷淋水和燃油在排气管道中积存;
★④ 排气系统中应设置弯管类似结构用于吸收、补偿整个试验段出口到消声塔之间管路产生的热膨胀量,其设计及选型应能满足试验器最高运行温度、压力条件下的管道变形补偿能力;
⑤ 排气系统应考虑未汽化冷却水的排泄问题以及排气和排水的除油问题,以达到规范条款规定的污染物排放标准的要求;
★⑥ 排气管道应具有良好的密封性,以避免排气的泄漏;
⑦ 排气系统应避免当一个台位开展试验时排气通过消音器反窜至另一个台位。
3)技术指标
★① 主流排气
排气温度:喷淋段前排气最高温度不低于1800K(此时排气流量5kg/s,压力3MPa),喷淋段后排气温度不高于573K;排气压力:背压阀前最高3MPa,背压阀后约0.1MPa;最大排气流量:10kg/s(含喷水)。
★② 次流排气
排气温度:473K(未考虑与试验件换热的温升);排气压力:背压阀前最高3MPa,背压阀后约0.1MPa;最大排气流量:1kg/s(不含喷水)。
4) 关键设备指标
① 喷水降温段
建议采用多级喷淋方案以匹配不同的流量工况,根据工况流量大小可以独立开启喷淋支路,在保证降温效果前提下节省喷水流量;材质不低于304不锈钢。
② 阀门
阀门用于调节试验件进口压力;技术要求同进气系统。
③ 滑移段
滑移段用于排气系统的热位移释放和提供试验件安装轴向空间,应采用软密封结构,保证燃烧试验台出口下游燃气不产生泄漏,滑移长度≮0.6 m;材质不低于304不锈钢。
2.1.2.3 燃烧系统工位燃油系统
1)概述
燃油系统主要作用是为试验件提供一定压力、温度、流量和清洁度要求的燃油。燃油系统主要由油箱、油泵、燃油管道、油滤、燃油加温器、燃油冷却器、阀门、测量仪器仪表、金属软管和氮气反吹管道等组成。
在油箱内设置有液位计实时监控液位高度,对应燃油喷嘴主燃级和预燃级,在油箱之后,燃油系统分为两条供油支路,两条供油支路应能独立同时工作。
在油泵前设置油滤,用于对燃油进行过滤。供油管道末端与试验件总管接口间采用金属软管连接。供油管路末端同时与氮气系统相连,采用氮气用于喷嘴的吹扫。在试验件点火前燃油调节过程中以及喷嘴热防护试验燃油加热过程中,高温燃油经回油总管上的燃油冷却器冷却后再回至油箱。
燃油加温器位于燃油系统中,用于对常温燃油进行加温,主要由电加热器、调功装置、电缆及其控制系统等组成。
燃油冷却器用于利用冷却水将高温燃油冷却至常温。
氮气反吹管道用于喷嘴吹扫,主要由氮气源、管道、阀门和测量仪器仪表等组成。
由于用气量较少,所以采用氮气瓶组供气。氮气经过气瓶所带的减压阀降压之后再进入氮气供气总管,之后氮气分为两路,分别供至主燃级供油管道、预燃级供油管道。氮气供气总管和各支路供气管上设置有手动开关阀用于氮气管路的开启和切断。设置开关阀用于远程控制通断,设置止回阀用于防止下游介质反窜。
2)功能要求
① 燃油系统总功能要求:
a) 系统应具备可靠的远程和现场手动切断功能,能在发生意外而需紧急停止供油时,可在3秒的内将燃油供给快速完全切断;
b) 系统工作过程中不允许有燃油泄漏;
c) 可灵活、便捷地对燃油的流量在招标人要求的范围内进行连续调节;
d) 油泵进口管路和出口管路应分别设有油滤,确保燃油足够清洁;
e) 油泵间内的电机、阀门和仪表等带电设备应具备至少d IIA T3等级的防爆功能;
f) 油滤前后设有压差指示,用于监测过滤器是否堵塞;
g) 系统应具备超压泄压及反压过高时止回的功能;
h) 氮气反吹压力应高于喷嘴反压,确保不会出现燃油倒流现象。
② 燃油加温器功能要求:
a) 加温器出口温度可调,远程控制;
b) 加温器采用闭环控制,试验过程中能有效保持温度恒定;
c) 加温器出现超温、超压和通过流量小于流量下限等异常现象时可报警提示和自动保护;
★d) 燃油加温器不得出现结焦或积碳等情况;
★e) 燃油加温器的防爆等级应不低于d IIA T3;
▲f)加温器出口温度控制精度:≤±2K;
g) 加温器温升速率:≮15K/min;
h) 加温器加热效率:≮85%;
3)技术指标
① 燃油系统总技术指标:
a) 试验件进口最高供油压力:≮8MPa;
b) 主燃级燃油流量15~150g/s,预燃级燃油流量0~50g/s,两条油路最大流量下不同时工作,总供油流量不小于150g/s;
c) 过滤精度:泵前≤100μm,试验件入口≤5μm;
d) 试验件进口燃油流量控制精度±1%FS,流量测量精度±0.5%FS;
e) 油箱容积应满足连续3小时试验需求;
f) 试验件入口处氮气最高压力:≮3.5MPa;氮气温度:常温。
② 燃油加温器技术指标:
主燃级燃油流量:15~150g/s,预燃级燃油流量:0~50g/s;加温器进口温度:常温(环境温度,最低按273K);加温器出口最高温度:430K;加温器进口最高压力:≮10MPa。
③ 燃油冷却器技术指标:
燃油最高进口压力:≮10MPa;燃油最高进口温度:430K;冷却水进口压力:1MPa;冷却水进口温度:305K(最高);冷却水出口温度:≤323K;冷却水流量具体值由投标人确定。
4) 关键设备指标
① 油箱
油箱用于短内存储燃油,技术要求如下:
a) 容积:应满足最高负荷工况连续3小时试验需求
b) 配置液位计
c) 主体材质:不低于304不锈钢
② 油泵
油泵用于将燃油进行增压,技术要求如下:
a) 工作介质:航空煤油
b) 型式:变频泵
c) 工作温度:常温
d) 最高工作压力:≮10MPa
e) 防爆等级不低于ExdIIBT3
③ 阀门
阀门用于调节燃油压力和流量,技术要求如下:
a) 具备压力自动设定功能
b) 耐压:≮10MPa
c) 流量、压力调节稳定度:≤ 1%
④ 质量流量计
流量测量采用科式力质量流量计,技术要求如下:
a) 工作介质:航空煤油
b) 工作温度:常温
c) 耐压:≮10MPa
d) 测量精度:不低于0.5%
e) 输出信号:4 mA~20 mA或0~5 V
f) 主体材质:不低于304不锈钢
2.1.2.4 燃烧系统工位冷却水系统
1) 概述
① 供水分为高压喷淋水供水和低压循环水供水,高压喷淋水主要用于通过试验件出口喷淋段直接喷入高温排气管道,将高温空气或燃气的温度喷淋冷却至573K以下。低压循环水主要用于试验件出口测量段、转接段和出口测量感头(如水冷形式的总压耙、热电偶耙和燃气取样耙等)。
▲② 冷却水系统包括上水泵、过滤器、回水阀、进水阀、止回阀、手动阀、管路、管道支架、测量仪器仪表及金属软管等。
③ 高、低压冷却水水源为室内两台独立的水箱,冷却水采用多级离心泵进行加压,水泵后一部分冷却水通过回水调节管道回至泵前,另一部分进入供水总管。各支路循环水回水管道最后汇总至总回水管道上,最后回至水箱。
2) 功能需求
▲① 可对喷水流量和循环水流量进行远程控制和灵活调节,以适应不同燃气/空气参数(温度和流量)的需求;
▲② 可对进水的压力、流量、温度和回水的压力、温度等参数进行监测;
③ 喷水雾化和降温效果好,确保管道不会出现热腐蚀;
④ 喷淋不会造成排气管道内部大量积水和倒流;
★⑤ 管道超压时具备自动泄压保护功能。
★⑥ 须配备相应的PVC管从水源处引水,并须为两台水箱配备液位计,具备通过监控液位高度变化的及时自动蓄水功能。
3) 高压冷却水技术指标
▲① 高压水用户进口处最高供水压力:≮4MPa;高压喷淋水流量具体值由投标人确定;高压循环水回水温度:≤50℃;
▲② 水箱须采用不锈钢材质,须设置上水和回水过滤器,容积须至少满足连续3小时试验需求,须采用散热器对循环水回水进行降温,温度控制在合适范围后再回至水箱。
4)低压冷却水技术指标
▲① 低压冷却水系统管道工作压力:≮1MPa;低压循环水流量具体值由投标人确定;低压循环水回水温度:≤50℃;
▲② 水箱须采用不锈钢材质,须设置上水和回水过滤器,容积须至少满足连续3小时试验需求,需对循环水回水进行降温,温度控制在合适范围后再回至水箱。
5) 关键设备指标
① 水泵
水泵用于将冷却水进行增压,技术要求如下。
a) 型式:离心式水泵
b) 供电电压:380 V
c) 核心件材质:不低于304不锈钢
② 过滤器
过滤器用于将进入水箱的上水和回水进行过滤,技术要求如下:
a) 具有耐酸、耐碱、耐低温性能;
b) 最高工作温度:不小于100摄氏度;
c) 过滤精度:不小于0.2mm。
③ 阀门
阀门包括开关阀门和调节阀门,分别控制水路的通断和流量、压力调节,技术要求如下:
a) 开关阀泄漏等级:零泄漏
b) 调节阀调节精度:不低于2%
c) 调节阀泄漏等级:不低于Ⅳ级
d) 阀门具备状态反馈功能
e) 执行机构类型:电动
f) 主体材质:不低于304不锈钢
④ 流量计
流量计用来计量冷却水量,技术要求如下:
a) 类型:体积式
b) 精度等级:不低于1.5级
c) 主体材质:不低于304不锈钢
2.1.2.5 调台试验件参数需求
燃烧系统的调台试验件包括燃烧测试段、涡轮导叶测试段试验件和平板发汗冷却测试段试验件,具体设计参数需求如下:
1) 燃烧测试段参数要求
★① 燃烧测试段须包括前测量段、燃烧室和后测量段三部分,下图为燃烧测试段示意图,仅作参考;
图2 燃烧试验件整体结构设计示意图
▲② 直径为200mm左右,能承受4MPa压力的管路,主要包括进气段(含扩压段)、收敛段(包括夹层水冷)、出气段和高温背压阀门,在燃烧室前后设有测量段,在测量段上留有安装传感器的底座,后测量段采用水冷,保证测量段在燃烧室出口温度达到1800K时能稳定工作,不出现变形、烧红的现象;
③ 后测量段上布置的测温热电偶须采用气冷方式,以保证其不被烧毁;
▲④ 整体压力、温度、流量等稳态数据采集通道不少于180路,动态数据采集通道不少于20路;
⑤ 燃烧室的点火装置须采用电弧点火,喷嘴设计、燃油流量调节须兼容点火试验研究;
★⑥ 燃烧室须设计为矩形段,两侧与顶部均须开有光学观测窗口,3处光学窗口须相互处于垂直关系,且须在工作温度处在1200K以下时,耐压能力不低于1.5MPa,且光学窗口具备防油雾污染和碳烟污染功能;
▲⑦ 测试试验段的尺寸约为截面尺寸120mm*100mm,轴向整体长度(含预留长度)须不少于4m(前测量段长度不少于600mm,燃烧室长度不少于800mm,后测量段长度不少于500mm),其中进入前测量段之前的进气管段须设计为伸缩段,该段的长度可在1m的范围内灵活调整;
▲⑧ 燃烧室须满足3MPa常温工况气密性测试,并保压1小时,漏气量须不大于0.2%。
2) 涡轮导叶测试段试验件要求
▲① 涡轮导叶测试件的叶片数目不小于7个,其中设计有内冷通道和气膜孔核心叶片不少于3个,核心叶片须安置在扇形段中间区域,并在两侧安置有陪衬的实心叶片模拟边界效应;
② 涡轮导叶测试件两侧适宜位置须开有光学观测窗口,以满足光学测试和红外测温需要;
③ 光学窗口的耐压强度不低于1.5MPa,耐温程度不低于1200K,且光学窗口须具备防油雾污染和碳烟污染的功能;
▲④ 陪衬实心叶片的长期运行最高耐受温度须不低于1200K,核心气膜冷却叶片的长期运行最高耐受温度须不低于1500K;
⑤ 中间核心叶片表面须采用打孔方式布置耐高温热电偶测点,测点布置方式须首先保证在叶片径向中截线上吸力面和压力面两侧适宜数目的均匀布点,并在其余区域遵从主流方向叶片中心区域密集、叶片尾缘区域稀疏的布置方式,整体温度测点数目不少于40个,且相邻热电偶测点之间不产生干涉效应;
⑥ 在打孔布置热电偶测点后,须在叶片表面喷射耐高温涂层,以保证叶片表面的平整度,不对流场造成干扰;
⑦ 叶片前后须采用周向截面均匀布点的压力采集方式;
⑧ 热电偶测点和叶片前后压力测点引线须从适宜位置引出,在保证密封性的同时,并保证采集信号的稳定性与精确性。
3) 平板发汗冷却测试段试验件要求
① 测试段总长须不小于1.3m,其最前部为渐缩过渡段,宽截面与燃烧室出口截面相转接,另一侧窄截面与其整流过渡段相接,之后为本体测试段,其整体示意如图3所示;
② 本体测试段为矩形通道,高度和宽度分别不小于90mm和60mm,其应可以与其余管段分开组装,其中通道一侧须安置有蓝宝石光学窗口,便于通过红外热像仪测量另一侧多孔介质表面的温度分布,另一侧的多孔介质为陶瓷基复合材料(CMC),须安置在承力样品架上,与承力支架相接的壁面须为一定耐温材料,且导热系数须不大于0.8W/(m?K)。除必要承力区域外,多孔介质测试件本体需要与其余区域留有间隙,以避免横向导热影响;
③ 多孔介质测试样品本体后部须设计有冷却剂增压室,其与样本本体之间应采用特定支撑框架相连接,须支持容纳不同的多孔样品厚度,并保证其间密封性;
④ 多孔样品表面须均匀安置不少于4个测温热电偶,其内部沿不同厚度位置须安置不少于4个测温热电偶,另须在增压室内安置一个热电偶以监控冷却气流温度;
图3 发汗冷却试验件整体结构设计示意图
⑤ 在测试多孔样品段进出口两侧须安置有压力探针,测量获得进口和出口总压。
2.1.2.6 燃烧实验工位测量系统
须根据上述燃烧实验台设计方案和相应调台试验件的参数测试需求,建立合理的测量系统,并须与试车控制系统相集成。
2.2 喷雾实验系统
2.2.1 喷雾实验系统总体技术指标参数 (含雾化试验段和喷嘴试验件设计)
★ 空气流量1kg/s;空气温度:常温~473K;燃油总流量:≮110g/s; 燃油压力:≮7MPa。
2.2.2 喷雾实验系统详细技术指标参数
2.2.2.1 功能需求
喷雾实验系统主要由进气系统、排气系统、燃油系统、雾化箱系统及测量系统等组成,可开展燃油雾化试验。
进气系统主要用于气液组合喷嘴用气,排气系统设置油气分离器,分离出液态油雾,再通过后端抽吸泵将气体抽至室外,需考虑油雾污染视窗。
试验件安装在雾化箱内进行试验,由箱体、门、光学玻璃、排风管、排油管等组成。喷雾试验台需测量喷雾的周向不均度,并包含两路油路。
2.2.2.2 技术指标
空气流量1 kg/s;空气温度:常温~473 K;燃油流量:100 g/s; 燃油压力:≮7 MPa;雾化箱拟定为圆柱形体,内径尺寸不小于500 mm,总长度不小于1800 mm。
2.2.2.3 调台试验件参数需求
喷雾实验系统的调台试验件为雾化试验段和喷嘴试验件,具体设计参数需求如下:
★① 雾化试验段应具有良好密封性能,须保证带背压测试环境,最低背压不低于0.3MPa,雾化测试腔体末端需要加排气系统;如做高温空气下的燃油雾化实验,需在排气管路加上换热器;
★② 喷嘴在腔体内部实现三维调节移动,调节精度±0.1mm;
③ 光学测量窗口为光学石英玻璃,视窗数量为4个,单个光学视窗面积不低于0.0314m2;
④ 试验段须仿制单头部设计,同时含有喷嘴与旋流器,其中喷嘴试验件的位置应可以灵活调整;
⑤ 旋流器进气须分为两路气流独立控制,以保证气压灵活调节,其中测点段压差须不大于10kPa;
⑥ 燃油的流量精度不低于0.5%;
⑦ 喷雾燃油温度加热温度不低于100℃,雾化腔体内加热温度不低于100℃。
2.2.2.4 喷雾实验工位测量系统
须根据上述喷雾实验台设计方案和相应调台试验件的参数测试需求,建立合理的测量系统,并须与试车控制系统相集成。
2.3 半物理仿真实验系统
2.3.1 半物理仿真实验系统总体技术指标参数 (含基底建设和调台试验件设计)
★1) 主流最大流量3kg/s,主流最高进气压力2.0 MPa,主流最高温度不低于500K;
★2) 二次流最大流量1.0 kg/s,二次流最高进气压力2.0 MPa;二次流进气流量为0.8kg/s时,最高进气温度不低于600K,且二次流需要留有三路调节气路,其中主调节流路流量不低于0.5kg/s,次级调节流路流量不高于0.2kg/s,末级调节流路流量不高于0.1kg/s;
▲3) 须有专门的气路用于轴承油气混合润滑系统密封,流量不低于0.1kg/s;
▲4) 须采用电主轴驱动方式,并须有专门的滑油循环系统用于冷却高速转动轴承;
▲5) 空气路质量流量计的精度要求为一级精度;
★6) 最高空载转速不低于30000 rpm,最大可承载轮盘试验件半径不小于400mm;
★7) 当承载轮盘试验件的最大半径为350mm时,最高稳定转速不低于15000 rpm;
▲8) 须满足下表工况校验参数:
表3 转动载荷参数需求表
序号 | 试验件半径(mm) | 转速(r/min) | 备注 |
1 | 0 | 30000 | 空载 |
2 | 300 | 20000 | 安置实心转盘件 |
3 | 350 | 15000 | 安置实心转盘件 |
4 | 400 | 10000 | 安置实心转盘件 |
▲9) 电机等安装须坐落在稳固的混凝土基台上,满足正常运行过程种振动值小于0.1mm,且设计转速点应避开一阶、二阶和三阶临界转速;
▲10) 须考虑与旋转盘腔换热试验件和旋转篦齿封严试验件的兼容接口,后续可拓展开展相关换热试验测试;
11) 主体设备长度不小于4m,宽度不小于2m;
★12) 须构建针对旋转涡轮叶片冷效的半物理仿真系统,将测试所得二次流流量参数作为实时边界输入,快速评估动叶冷效。
2.3.2 半物理仿真实验系统详细技术指标参数
1)物理试验台主要由进排气系统、动力系统、设备支撑系统、润滑系统、冷却水系统和控制系统组成,可开展涡轮轮缘封严、旋转盘腔换热、旋转篦齿封严旋等试验研究,研究所获得的二次流空气系统流量参数和盘腔表面换热系数等可作为旋转涡轮叶片冷效研究的半物理仿真输入条件。
★2)半物理仿真系统须能够结合物理实验台架系统开展发动机旋转叶片冷效系统研究,通过采集物理实验台架上布置的各种传感器信号如流量、压力、温度信息,通过实时仿真机开展半实物仿真分析。该系统需采用实时仿真系统,通过运行被试对象数学模型实现对被试对象的仿真分析。
2.3.2.1 物理实验台进排气系统
1)进排气系统需满足试验件供气压力和流量的需求,设置截止阀,泄压阀和调节阀等。
2)主流最大流量3 kg/s;主流最高进气压力2.0 MPa;主流最高温度不低于500 K;二次流最大流量1.0 kg/s;二次流最高进气压力2.0 MPa;二次流需要留有三路调节气路,以满足流量精细化调节;须有专门的气路用于轴承油气混合润滑系统;空气路质量流量计的精度要求为一级精度。
3)主流进气系统须提供试验所需的均匀进气来流,调节进气压力、测量进气流量,主要由进气消声器、流量管、前扩压段、进气节流装置、后扩压段、稳压箱(内含蜂窝器、整流网)、收敛段、可移动支撑架、传感器及探针组成,须满足指标如下:
a) 进气节流调节精度:不低于1%;
b) 出口湍流度:不大于2%;
c) 总压不均匀度:不大于5%;
d) 进气降噪量:塔口噪音≤85dB(A);
e) 整流元件材质:不低于304不锈钢;
f) 筒体主体材质:不低于10Cr17。
4)排气系统收集轮缘封严试验件出口气流,将出口气流排入大气,同时起调节排气压力的作用,须满足指标如下:
a) 耐压:不低于0.4MPa;
b) 节流阀精度:不低于1%;
c) 排气降噪量:塔口噪音≤85dB(A);
d) 主体材质:不低于10Cr17。
2.3.2.2 物理实验台动力系统
▲1)动力系统需设计与试验件匹配的联轴器,满足试验件传动的需求;动力系统需预留对接旋转测量设备的接口,满足试验件转子测量的需求;动力电机功率不小于150 kW;输出最高空载转速不低于30000 rpm。
2)动力系统须由变频器、电机、测扭器、联轴器及底座、传感器等组成,满足转速控制精度为0.05%FS。
2.3.2.3 物理实验台设备支撑系统
设备支撑系统(设备支撑基底)用于为动力系统和试验件等部件提供稳定平整的安装平面,技术要求如下:
1) 基底支撑系统设计尺寸需满足动力系统和试验件的安装尺寸要求;
2) 基底支撑系统需设计T型安装导轨,方便设备安装和紧固;
3) 基底支撑系统表面加工及现场安装精度,整体高度跳动不超过1mm;
4) 基底支撑系统的安装实施,包含现有场地安装所需的土建设计变更和实施;
★5)基底支撑系统需满足试验设备运行的强度要求,避免支撑设备发生沉降或变形。
2.3.2.4 物理实验台润滑系统
润滑系统主要由油箱、油泵、阀门、油滤、加温器、散热器、传感器、管路、管件等组成,主体分两路供给,每路流量5 L/min;两路压力、流量分别可调;滑油供油温度30~100 ℃。
2.3.2.5 物理实验台冷却水系统
冷却水系统主要为润滑系统提供冷却用水,主要由阀门、流量计、传感器、过滤器、管路、管件等组成。
① 冷却水需满足的技术指标如下::
a) 最大水量:≮5t/h
b) 最大压力:≮1.0MPa
② 阀门、流量计技术要求同燃烧系统冷却水系统阀门、流量计。
2.3.2.6 物理实验台动力电机控制系统
动力电机控制系统用于实现动力电机设备的供电和转速控制。
动力电机控制系统要求如下:
▲要求在线监视动力电机的转速、扭矩等参数;控制记录采样频率不得小于10 Hz;转速控制可以自动追踪目标转速;电机控制系统需实现紧急情况报警、应急处置等功能;操纵台上应设置独立的紧急开关。
2.3.2.7 物理实验台的调台试验件参数需求
半物理实验系统的调台试验件为涡轮轮缘封严试验件,具体设计参数需求如下:
① 试验件上部须设计有主流通道,通道径向尺寸须与试验件尺寸相适宜;
▲② 调台试验件半径尺寸(含假叶片)不小于350mm,试验件为转-静系盘腔,盘腔上缘须采用鱼嘴式封严结构,盘腔径向下部位置采用篦齿封严结构,二次流供气从静止盘中心位置供气,整体结构如图4所示;
图4 轮缘封严试验件整体结构设计示意图(不含一级半假叶片)
▲③ 涡轮轮缘封严试验件需要在静子和转子盘上安置一级半假叶片(含两级导叶和中间一级动叶),假叶片的高度取为真叶片高度的五分之一;
▲④ 涡轮轮缘封严试验件的设计须在15000 rpm参数以下满足转子动力学强度要求;
▲⑤ 静止盘表面的轮缘封严处、盘中心区域和盘底部区域须设置6处以上CO2浓度检测探针,其中轮缘封严位置不少于3处,且该系列探针须与排放测试系统相连接,获得稳定、精确的信号测试数据;
▲⑥ 静止盘表面须采用打孔方式布置压力探针和热电偶,在轮缘封严等转弯位置处较密布置测量点,除轮缘位置外,压力测点和温度测点均须等距布置,其中沿径向温度测点不少于5处,压力测点不少于10处,每处径向高度的周向均匀布置4个温度和压力测点;
▲⑦ 每处主流叶栅底部的轮缘壁面位置须沿周向均匀布置不少于15个压力测点;
▲⑧ 转子盘壁面须采用滑环引电器测温技术,测试数据须在15000 rpm参数以下保持稳定,且测量误差不大于2.5%;
⑨ 轮缘封严处的泄漏流量须不大于主流流量的6%,下部篦齿处泄漏流量须不大于主流流量的0.5%。
2.3.2.8 物理实验台测量系统
须根据上述物理实验台设计方案和相应调台试验件的参数测试需求,建立合理的测量系统,并须与试车控制系统相集成。
2.3.2.9 半物理仿真系统
系统功能须具备以下功能:
★① 须构建针对旋转涡轮叶片冷效分析的简化仿真模型,建立仿真模型与实际物理试验台的实时参数交互接口;
② 采用上下位机架构,上位机运行Windows操作系统,下位机运行 Linux实时操作系统;
③ 实时仿真系统支持三种硬件架构,包括工控机/ PCIe板卡、工控机/扩展套件+机箱+PXI/PXIe/CPCI板卡、机箱+处理器板卡+ PXI/PXIe/CPCI板卡;
④ 实时仿真系统支持多核并行运行,每个核心可以运行不同仿真模型,且每个仿真模型可设置不同的仿真步长
⑤ 具有丰富的IO板卡和总线板卡资源,结合调理设备能够实现物理实验台上传感器信号的采集
⑥ 支持Simulink模型的剖析、代码生成、编译和加载;具有板卡驱动库,无缝集成与Simulink环境,在上位机中可实现对下位机中IO和总线板卡的资源配置、调度;
⑦ 支持符合FMI规范的模型联合仿真,支持AMEsim、Simpack、C++等不同种类模型;
⑧ 具有仿真监控管理软件,基于该软件可个性化搭建人机交互界面,能够实现工程管理、模型管理、数据记录、在线调参、曲线显示等功能,支持用户自定义监控界面,提供表格、曲线、仪表等控件;
⑨ 实时仿真系统软件采用B/S架构支持多用户分布式监控;
⑩ 具有代码编译控制软件,能够将上位机中搭建的非实时模型编译成下位机实时仿真系统可执行的文件,并下载到下位机中运行。
2.4 3D打印台
2.4.1 3D打印台总体技术指标参数
★ 小型3D打印设备成型尺寸:160mm×160mm×200mm(W×D×H);大型3D打印设备成型尺寸:800mm×800mm×650mm(W×D×H)。
2.4.2 3D打印系统详细技术指标参数
2.4.2.1 小型SLM设备技术指标
1) 设备用途:此设备主要用于小尺寸复杂金属构件选区激光熔化成形。
2) 设备组成:主要有激光系统、扫描振镜系统、成形加工系统、控制系统、质量监控系统、气体循环过滤系统、数据处理软件系统等组成。
3) 最大有效成形尺寸:≥160mm×160mm×200mm(L×W×H)(不含基板,基板厚度≥20mm);
4) 可成形材料:适用于钛合金、高温合金、铝合金、不锈钢、铜合金等材料,提供不少于5类材料10个牌号的成熟材料工艺参数包,参数包用户可编辑、修改。
5) 设备可配置不少于3种刮刀,包括钢刮刀、橡胶刮刀、无磁刮刀等。
6) 激光系统
采用IPG品牌光纤激光器;激光功率:≥500W,输出功率范围:10%-100%,激光波长:1060~1080nm,M2<1.1;激光冷却方式采用水冷,实时监控水冷机状态,异常情况报警,水冷机控温精度达到±0.1℃。
7) 扫描振镜系统
采用Scanlab品牌振镜;采用F-theta lens聚焦; 光斑直径范围应≤70μm;X,Y轴的最大扫描速度:≥7m/s;全幅面尺寸95%校准点定位精度≤0.05mm。
8) 成形加工系统
① 采用下顶粉,单向变速铺粉;
② 铺粉层厚:20~100μm范围内可调;
③ 基板最高预热温度:≥350℃,提供设备预热实际温度监控视频;
④ 设备具备良好的气密性,采用静态密封设计,成型缸及Z轴在氩气保护下工作,打印过程中最低氧含量可控制在100ppm以内,Z轴运动机构全密封,避免粉末外溢;
⑤ 支持更小平台切换成形打印,成形尺寸不大于50mm×50mm×50mm,成型平台预热≥350℃,便于用户新材料研发,节约粉末;
⑥ 设备须具备一键铺粉、一键准备及一键打印功能,可根据初始设置参数自动完成设备准备工作并开始打印,全程无需人员干预,需提供证明资料;
⑦ 集成智能化精准送粉,支持用户自助选择,可实现自动根据当前打印截面智能调节送粉比例,有效减少粉末浪费,提供软件应用截图。
9) 控制系统
①采用PLC数字控制系统;
②采用安全控制器进行了安全回路的设计,安全继电器等级可达到SIL3级;
③具备网络接口,并能够实时反馈设备的运行情况如各轴扭矩,位置等信息。具有数据采集、显示、储存等功能;
④整机伺服控制均使用总线伺服驱动,传输速度快,可实现闭环控制,设备控制操作均使用触摸屏,方便快捷;
⑤自主研发设备控制软件,可依据分层切片结果控制激光器输出激光对金属粉末进行烧结,成形的主要工况可进行调节和记录,成形过程可全自动进行,提供软件著作权证书。
10) 质量监控系统
① 可实时监测、显示并记录零件成形关键信息,以上信息应至少包含平台温度、舱内温度、舱内压力、各轴扭矩和位置、打印进度以及成形舱内氧含量等;提供软件监控截图;
② 具有成型仓氧含量,压力异常报警功能,且压力超标时可自动泄压;
③ 具备自诊断故障功能,可实现实时监控并分级诊断,故障进行监测、记录,分析;针对不同故障影响程度分级处理,提高效率,避免设备停机;
④ 具备工作报表模块,可生成工作报表,工作报表包含零件信息、暂停信息、打印日志、操作日志、报警日志、工时记录、生产记录等,支持用户自由进行内容和筛选。工作报表可实现所有监控数据筛选至少任意2组以上数据对比分析,有利于客户质量分析对比追溯。提供工作报表及功能界面;
11) 数据处理软件系统
① 模型处理软件
a) 选用Magics最新版本模型处理软件;
b) 支持*.stl、*.amf、*.3mf、*.obj等多种格式导入导出;
c) 具备零件三角面片编辑优化功能,可实现对模型文件表面三角面片光滑、细化,以及重画网格;
d) 支持自动及手动生成支撑;能快速、简单、自动创建和处理各种不同类型的支撑结构,如点状、线状、网柱状、轮廓、肋状、锥形、树状及综合支撑,同时具备斜角支撑、支撑加厚、支撑投影区域缩放等功能,提供对应功能截图;
② 剖分软件
a) 选用自主研发剖分软件,具备至少2次版本迭代记录,能快速、自动生成切片数据,提供软件著作权证书;
b) 开放多项可编辑参数,便于客户优化工艺参数,获得性能更优的零部件,开放工艺参数设定界面,用户可自行编辑设定,包括切片厚度、扫描速度、填充间距、扫描策略等,并可单独对各个参数进行快速设定和控制;
c) 具备参数保护功能,可对已开发的参数可进行部分开放或隐藏。
d) 可以实现同一版不同零件变层厚打印,以及同一零件不同高度的变层厚打印,提供软件应用截图;
e) 具备平台、零件、综合、高效 4 种打印模式,同时可以自由调节零件的上表面区域、内填充区域、下表面区域的填充与外圈的扫描先后顺序,以及调节零件与支撑的扫描先后顺序,提供软件应用截图;
f) 可根据零件摆放角度精准识别划分上表皮、内填充和下表皮区域,每个区域可实现灵活选择只打印外圈、只打印填充以及同时打印外圈+填充三种模式,实现不同结构零件兼顾效率和质量的打印需求;
③ 自主研发离线工时计算软件,可实现离线状态下工时计算、路径预览、辅助路径查错等,离线工时计算软件需独立在设备工控机外的电脑中操作,避免占用设备打印,提供软件著作权证书;
12) 循环过滤系统
采用圆柱式滤芯三级过滤,滤芯级别不低于p3级别。设计有可注水滤芯箱,防止滤芯更换过程中发生自燃,确保操作人员更换滤芯过程安全,提供注水滤芯实物图。
13) 安全设计保障
a) 设备设计制造应符合 ISO、CE等标准,提供设计符合性证明材料并提供查询网址;
b) 有激光安全锁,确保设备正常运行时成形舱门不能打开;
c) 设备整机设计符合ATEX防爆标准,可安全处理活性材料,提供符合ATEX标准评估证明资料;
d) 防护窗应保证操作人员安全,安全等级≥OD4+,提供衰减系数安全等级报告;
e) 设备应有急停按钮,按下后设备立即停止运行;
f) 激光器安全合格出厂,整个激光防护系统安全可靠,通过第三方安全认证注册。
14) 附属设备耗材清单
表4 附属设备耗材清单-1
序号 | 辅助设备及耗材名称 | 数量 | 单位 | 技术要求 |
1 | 防爆吸尘器 | 1 | 台 | 功率(kW):≥2.2KW;电源(V/Hz):380/50V/Hz;最大风量≥318m3/h;吸入口径≥?40mm;前置水箱容积≥100L;过滤效率不低于99%;滤筒数量(个)1;滤筒滤材采用防静电覆膜滤材,提供防爆评估认证 |
2 | 真空干燥箱 | 1 | 台 | 电源电压:AC220V 50HZ;控温范围:RT+10-200℃;控温精度:0.1℃;波动率:±1℃;最高真空度:133Pa;工作环境:5-40℃;内胆尺寸≥415*370*345mm |
3 | 循环过滤滤芯工装 | 2 | 套 | F9+p3换粉滤芯工装 |
4 | 普通钢刮刀 | 2 | 根 | 匹配所投设备 |
5 | 橡胶刮刀 | 2 | 根 | 匹配所投设备 |
6 | 钛合金基板 | 2 | 块 | 匹配所投设备 |
7 | 不锈钢基板 | 2 | 块 | 匹配所投设备 |
8 | 高温合金粉末 | 35 | KG | |
9 | 钛合金TC4粉末 | 40 | KG | 粒径要求15-53微米 |
15) 安装调试及验收
① 安装调试:卖方负责设备安装调试;签订合约后,卖方需了解客户的客观安装条件,确定设备的具体安装位置是否符合设备使用要求。
② 验收:设备在买方现场进行最终验收,终验收包括但不限于设备实物验收、设备调试验收和试加工验收,终验收报告经双方代表签字有效;
③ 培训:在买方安装现场对相关人员进行不少于3个工作日的技术培训,培训包括设备使用和维护技术培训,使买方人员能够独立正确使用、维护设备,并具备常见故障分析和排除能力。
16) 技术及售后服务
① 设备制造商具备一定的工艺研发实力,能够有能力配合学校进行部分工艺试验及研究,提供近一年不少于5份所投设备与高校签订的合同复印件和中标通知书;
② 所投同系列设备经过技能大赛应用验证,成熟可靠,满足国家及以上技能大赛对增材制造设备技术要求,提供设备参与应用技能大赛证明材料。
③ 设备自终验收后,进入质量保证期,质量保证期整机为1年(自用户最终验收签字生效之日算起);
④ 制造商具备完善的履约能力,可协助客户完成成果验证,包含产品加工、原材料粉末生产以及检测能力进行评估,具备产品加工生产线能力、具备原材料金属粉末生产线能力、具备增材制造检测实验室(提供加工生产线现场照片、相关证明材料以及官方宣传资料、检测实验室认证)
2.4.2.2 中大型SLM设备技术指标
1) 设备用途:此设备主要用于大尺寸复杂金属构件选区激光熔化成形。
2) 设备组成:主要由光学系统、冷却系统、成形加工系统、控制系统、质量监控系统、循环过滤系统、取件系统、粉末循环系统等组成。
3) 适用材料:钛合金、高温合金、铝合金、不锈钢等材料,可提供不少于4类材料10个牌号的成熟材料工艺参数包,且参数用户可编辑、修改。
4) 光学系统
① 激光器采用单模光纤激光器,采用IPG光纤激光器;
② 激光数量≥6,单台激光功率≥500W,激光波长1060~1080nm,M2≤1.1;
③ 采用Scanlab品牌intelli系列扫描振镜,重复精度≤2μrad,非线性精度≤3.5mrad/44°,响应快,跟随误差≤0.32ms,电机采用数字伺服控制抗干扰能力强,具备自诊断功能,可读取振镜状态、温度报警反馈,具备长
运行稳定性;
④ 采用F-theta lens聚焦,聚焦光斑直径满足70μm-100μm范围内;
⑤ 扫描模块可以覆盖到整个成形区域,并保证每处烧结质量的一致性,同向试棒抗拉强度多激光搭接区域最低性能不低于单激光区域平均值95%,全幅面尺寸95%校准点定位精度优于0.05mm,搭接区域尺寸偏差不高于±0.1mm;
⑥ Ⅵ具备振镜精度校准功能,可实现单振镜精度校正和多振镜拼接精度校正,通过扫描仪/影像仪等硬件,与配套软件相结合,并开放相关权限,用户可实现振镜精度和拼接精度的自主校正;
5) 冷却系统:
激光器冷却方式采用水冷,配置水冷机,实时监控水冷机状态,异常情况报警,水冷机控温精度可达±0.1℃。
6) 成形加工系统:
★a) 最大有效成形尺寸:≥800mm×800mm×600mm(W×D×H)(不含基板,基板厚度≥100mm);
b) 设备须采用合理两工位设计,清粉及取件工位集成一体,设备集成度更高,可实现成型、清粉和取件功能,投标时提供证明材料;
c) 成形缸体、平台及驱动单元整体采用静密封,成形缸和驱动系统都置于惰性气体空间内,保障成形过程稳定及设备安全性;
d) 可配置刚性刮刀和柔性刮刀,根据所做零件的材质和形状选用合适的刮刀以实现最佳成形效果;
e) 采用龙门式刮刀架结构,单根刮刀实现双向/单向铺粉,采用一侧落粉一侧顶粉式方案,结构可靠性和容错率高,具备相关专利,提供相关专利证明;
f) 成形缸采用结构优化设计方案,3D打印一体成形,非拼板方案,不锈钢材质,具备长使用稳定性;
g) 成形平台承力基座采用铸件,保证结构设计可靠性和长期运行稳定性;
h) 具备基板预热功能,预热温度可达100℃;
i) 设备具备良好的气密性,打印过程中最低氧含量可控制在100ppm以内,打印过程中惰性气体消耗低于10L/min(工况下);
j) 送粉方式采用上落粉,可实现不停机不间断加粉,落粉模块可拆卸,整体吊装,方便粉末更换、清理;
k) 供粉舱体积≥150L,供粉舱配置探杆式物位计,可对供粉舱内粉末量进行实时监测、实现缺粉检测及预警报警,提供供粉舱体积设计说明及粉末状态软件监控截图;
l) 具备动态多段变速铺粉功能,可智能识别打印截面和非打印截面,自动调节刮刀铺粉速度,保证铺粉质量和效率;
7) 控制系统:
① 采用PLC数字控制系统,能够实时反馈设备的运行情况如各轴扭矩,位置等信息,具有数据采集、显示、储存等功能;
② 采用高质量电机、伺服系统,保证控制系统运行稳定性;
③ Z轴配备光栅尺,可实现零件打印过程实时高度检查,具备异常报警功能;
④ 整机伺服控制均使用总线伺服驱动,传输速度快,可实现闭环控制;采用安全控制器进行了安全回路的设计,安全继电器等级可达到SIL3级;
⑤ 设备集成UPS电源可实现断电保护,可自动保存当前打印数据,供电后第一设备可正常工作;
⑥ 设备可实现一键铺粉、一键准备、一键打印、一键移缸功能,可根据初始设置参数自动完成设备准备工作并开始打印,可实现成形缸在成形位和取件位的快速转移,提供设备软件功能截图;
⑦ 控制软件具有独立著作权,能实现设备增材打印、控制、监控等功能,软件控制系统自动化程度高、人机交互友好,方便完成对设备的运动控制、送粉、过滤和其他功能设置,提供软件著作权证书。
8) 质量监控系统:
① 实时监测、显示并记录零件成形关键信息,以上信息应至少包含平台温度、舱内温度、舱内压力、各轴扭矩和位置、零件成形图像、打印进度以及成形舱内氧含量等,提供软件监控截图;
② 具备成形平台漏粉和漏液检测,及时识别相关风险,保证设备安全运行,提供实现该功能硬件配置及说明;
③ 内置高清相机,可采集每层铺粉后和打印后的照片,实现铺粉质量实时监控,并可自主处理多种铺粉异常;如缺粉,可自动执行重铺,如出现刮刀卡停、小区域塌陷等,可及时报警停机,并记录状态信息,便于质量追溯;
④ 内置录像机,可实现打印过程的视频监控,可通过MES实现远程视频监控,提供录像机硬件及监控证明资料;
⑤ 可根据打印照片进行打印过程三维重建,可实现离线端和在线端的重建,并且在重建的三维立体模型中识别缺陷区域,如缺粉、错位、扫描缺失等,提供此功能操作应用视频;
⑥ 成形舱配置双氧、双压力传感器,具备传感器冗余设计,保证数据真实性,具有氧含量及压力异常报警功能,且压力超标时可自动泄压;
⑦ 具备氩气实时消耗和累计消耗显示和记录功能,可及时观察到氩气消耗异常和帮助用户统计每炉零件氩气消耗量,便于氩气使用成本核算,提供软件监控截图;
⑧ 具备工作报表模块,可生成工作报表,工作报表包含零件信息、暂停信息、打印日志、操作日志、报警日志、工时记录、生产记录等,支持用户自由进行内容和筛选。工作报表可实现所有监控数据筛选至少任意2组及以上数据对比分析,有利于客户质量分析对比追溯,提供工作报表及功能界面。
9) 循环过滤系统:
① 自研循环过滤系统,采用模块化设计,可单独进行拆装维护,采用烧结板过滤器,具有较长使用寿命,可满足设备连续运行需求,过滤系统应具备自动清洁滤芯的功能;
② 过滤系统具备氧含量、温度、压力监控,保证使用安全;
③ 具备安全处理设计,并配置相应工装,可实现湿化惰化处理,保证使用和操作安全,避免设备清理及维护时可杜绝燃爆危险;
④ 配置备用灰桶,打印过程中可不停机更换灰桶,具备灰桶自动洗气功能,保证更换灰桶不破坏成形气氛,保证打印连续性。
10) 取件系统:
① 设备集成一体化取件舱,取件舱具备密封性,可实现惰性气氛保护下的清粉;
② 取件舱具备氧含量、压力和温度传感器,可实现取件舱的压力、氧含量和温度实时监控;并具备安全互锁逻辑,超压自动泄压,负压自动补气,氧含量高的自动气体置换和高氧高压报警等;氧传感器≥2个,具备冗余配置,保证安全使用;
③ 具备双位脚踏开关设计,一个负责成形平台移动,一个负责物料机启停,操作便捷;
11) 数据处理软件:
① 模型处理软件
a) 选用最近版本Magics模型处理软件;
b) 支持*.stl、*.amf、*.3mf、*.obj等多种格式导入导出;
c) 具备零件三角面片编辑优化功能,可实现对模型文件表面三角面片光滑、细化,以及重画网格;
d) 支持自动及手动生成支撑;能快速、简单、自动创建和处理各种不同类型的支撑结构,如点状、线状、网柱状、轮廓,肋状,锥形,树状及综合支撑,同时具备斜角支撑, 支撑加厚,支撑投影区域缩放等功能;
e) 具备不少于10种基础的CAD文件编辑功能,如删除面、锥化面、镜像、圆角、倒角、拉伸、偏移、镂空、布尔运算、适配孔等,完成编辑后可直接导出STP等CAD文件格式;
f) 具备零件信息修复页,可实时查看模型文件上现有错误,提供软件界面证明材料;
g) 具备不少于11种打印前零件分析功能,必须具备零件碰撞检测功能,提供软件界面证明材料;
h) 自动摆放可设置避免重叠区域摆放设置,提供软件功能界面截图;
② 路径规划切片软件
a) 制造商自主研发路径规划切片软件,具备至少2次版本迭代记录,与设备控制软件相兼容,能快速、自动生成切片数据,提供软件著作权证书;
b) 可以实现层厚为倍数关系的同一版不同零件变层厚打印,以及同一零件不同高度的变层厚打印,提供软件应用截图;
c) 可实现多光之间的分割线可视化,支持自由拖动切割线的位置,满足同一材料参数包对不同结构零件的打印需求,提供软件应用截图;
d) 具备多种扫描策略可选,具备细化分区功能,可实现多光同时出光扫描,同时保证打印质量;
e) 在单个激光可覆盖单个零件区域时,可以指定使用单个激光打印,避免搭接;
f) 具备智能分区功能,可实现速度优先搭接-高效率扫描、速度优先搭接-高质量扫描、质量优先搭接-高效率扫描、质量优先搭接-高质量扫描四种智能分区扫描模式,在保证打印质量的同时实现多光同时出光打印零件,提供软件应用截图;
g) 可根据零件摆放角度精准识别划分上表皮、内填充和下表皮区域,每个区域可实现灵活选择只打印外圈、只打印填充以及同时打印外圈+填充三种模式,实现不同结构零件兼顾效率和质量的打印需求,提供软件应用截图;
h) 外圈可实现高质量扫描和高效扫描两种模式,零件外圈可自由选择是否划分填充外圈、上表皮外圈和下表皮外圈,同时表皮外圈可灵活选择与填充区域外圈搭接、与填充区域外圈不搭接、被填充外圈重熔、输出轮廓外圈,输出区域外圈等多种外圈扫描模式;可根据零件类型自由选择外圈模式,提高零件打印后的表面质量;
i) 软件具备 none 填充、条带填充、棋盘填充以及轮廓填充四种填充模式,其中 none 填充模式下包含不少于 3 种填充扫描模式,条带填充模式下包含不少于 15 种填充扫描模式,棋盘模式下包含不少于 23 种填充扫描模式,轮廓填充模式下包含不少于 31 种填充扫描模式,供用户在不同使用场景下兼顾打印效率和打印质量的打印需求;
③ 制造商自主研发离线工时计算软件,与设备控制软件相兼容,可实现离线状态下工时计算、路径预览、辅助路径查错等,提供软件著作权证书;
④ 所提供数据处理软件均为正版合法软件,提供软件合法授权或著作权。
12) 粉末循环系统:
a) 可实现打印过程中溢粉粉末自动回收、筛分和供应,和打印完成后取件舱粉末的高效回收;打印过程中与主机可通讯,实时检测溢粉桶状态和储粉桶状态,自动实现粉末回收与供应,无需人为干预;
b) 粉末循环系统选用分体式方案,筛粉机、物料机、供粉机均可独立工作,避免单一模块故障影响整体系统工作;筛粉机、物料机、供粉机均为制造商自主研发,可与设备主机兼容;
c) 筛粉机1套,用于回收粉末的自动筛分,采用触摸屏智能控制,超声波与机械振动筛分相结合,筛分效率可达到50L/h,具备惰性气体保护系统保证粉末质量,可实现人粉隔离。
d) 物料机1套,用于粉末全封闭式收集,人粉隔离,确保操作人员安全,实现打印结束后方便快捷回收粉末,粉末回收效率钛合金可达到1000kg/h;
e) 供粉机一套,可自动为打印设备补充粉末,粉末供应全过程采用惰性气体保护,供粉机可和主机进行互联,实时获取主机储粉桶的料位,实现不停机加粉,粉末供应效率不低于130L/h;
f) 配置提升搬运车一台,用于物料和粉末的搬运,提升车载重不低于1.5吨,高度不低于3m;
g) 粉末筛粉、回收及供应均安全可靠,筛粉机、物料机及供粉机均符合CE和ATEX防爆评估提供证明资料;
h) 真空干燥箱1台:容积不小于215L,控温范围:RT+10-200℃;控温精度:0.1℃;波动率:±1℃;最高真空度:133Pa;工作环境:5-40℃;内胆尺寸:560*600*640mm;搁板:3块(独立控温);
13) 耗材清单:
表5 附属设备耗材清单-2
耗材名称 | 数量 | 单位 | 规格 |
钢刮刀 | 5 | 把 | 匹配投标设备 |
橡胶刮刀 | 20 | 把 | 匹配投标设备 |
龙门吊 | 1 | 套 | 匹配投标设备 |
不锈钢基材 | 2 | 块 | 厚度不小于100mm |
模块化粉桶 | 2 | 个 | 不小于150L |
模块化粉桶 | 1 | 个 | 不小于20L |
灭火器 | 1 | 个 | / |
钛合金基板 | 1 | 块 | / |
钛合金粉末 | 300 | KG | / |
高温合金粉末 | 500 | KG | 15-53微米 |
圆柱滤芯p3(灰桶) | 2 | 个 | 匹配投标设备 |
p3空气过滤器 | 2 | 个 | 匹配投标设备 |
防爆吸尘器 | 1 | 台 | 功率(kW):≥2.2KW;电源(V/Hz):380/50V/Hz;最大风量≥318m3/h;吸入口径≥?40mm;前置水箱容积≥100L;过滤效率不低于99%;滤筒数量(个)1;滤筒滤材采用防静电覆膜滤材,提供防爆评估认证 |
14) 安全设计保障:
① 设备设计制造应符合 CE安全标准,包括电气、机械、防爆指令标准,设备整机通过CE认证,提供符合CE标准认证证书及网站查询截图,以备核实;
② 设备整机设计符合ATEX防爆标准,可安全处理活性材料,整机通过ATEX防爆评估,提供符合ATEX标准评估提供证明资料;
③ 成形舱具备双层门设计,外部门上具有安全门锁,与激光器和运动轴有安全互锁;配备工业手套箱,实现人粉隔离;有急停按钮,按下后设备立即停止运行,保证操作和使用安全;
④ 物料机和取件舱安全互锁,两边的氧含量均达标时,物料机才会启动,保障粉末回收安全;
⑤ 成形舱观察窗具备三层防护玻璃,材质为两层钢化玻璃和一层防护玻璃,防护窗应保证操作人员安全,安全等级≥OD4+,提供衰减系数安全等级报告;
⑥ 整个激光防护系统安全可靠,具备针对激光防护系统第三方安全认可,提供激光器出厂合格证及激光防护系统第三方安全评估证明;
⑦ 设备顶部具有安全防护护栏,保证人员操作和调试安全;
15) 安装调试及验收
① 工作环境要求
② 电源:AC 380V,三相五线;
③ 设备可在环境温度15~30℃,相对湿度≤75%的环境下长稳定工作;
④ 安装调试:卖方负责设备安装调试;签订合约后,卖方需了解客户的客观安装条件,确定设备的具体安装位置是否符合设备使用要求;
⑤ 因学校场地因素受限,要求设备的尺寸整体外部尺寸不大于7米*5米*5米。
⑥ 验收:设备在买方现场进行验收,验收包括但不限于设备实物验收、设备调试验收和培训验收,验收报告经双方代表签字有效;
⑦ 培训:在买方安装现场对相关人员进行不少于10个工作日的技术培训,培训包括设备使用和维护技术培训,使买方人员能够独立正确使用、维护设备,并具备常见故障分析和排除能力;
⑧ 技术资料验收:随设备提供设备手册、设备操作及维护手册、设备电气原理图等。
16) 技术及售后服务
① 设备制造商具有专业售后服务及技术保障团队;
② 提供近三年投标设备具备销售同型号案例至少10台以上,提供同型号业绩及验收报告;
③ 设备自终验收后,进入质量保证期,质保期整机为1年,包含3次免费维保(自用户最终验收签字生效之日算起,用户指定维保);(投标时每增加1次免费维保加1分)每次维保
不低于12天,每次维保人数不低于2人,维保费用不高于6万元每次(投标时维保费每减少1万加1分)。
④ 在质量保证期内,投标人服务应及时有效,在接到买方故障信息后,要求24小时内响应,如有必要,48小时内维修人员到达现场,5个工作日内解决故障;
⑤ 设备保修期过后,制造商具备能力终生提供广泛而优惠的备件供应和技术支持。
17) 包装及运输:
包装箱应用新的坚固的木箱或铁皮箱,适于长途运输,防潮、防锈、防震、防粗暴装卸;适于陆(公路、土路)运输。
2.5 试车台控制系统
★试车台控制系统须涵盖燃烧系统、喷雾实验系统、半实物仿真实验系统、天然气系统、气源系统、后处理系统和排放测试系统等的电气、控制、数据采集和音视频监控记录等功能。
2.5.1 试车台控制系统总指标参数
电气系统主要用于给试验设备供电,控制系统主要用于控制、反馈试验台各类状态参数,并通过调节试验件进口流量、进口温度、转速等参数实现工况的模拟,数据采集系统用于试验台系统及试验件的压力、温度、流量等参数的测量、采集及显示,并实现数据的实时监视、处理、分析和管理,音视频系统主要用于完成对试验区域重点部位的视频监控。
★1) 各模块独立控制系统、远程控制,温度控制精度±3K,压力控制精度±1%FS,流量控制精度±1%FS;
▲2) 在远程采用热电偶测温时,温度测量补偿导线须不应过长而影响测温精度,其精度影响须不大于3℃;
★3) 采集通道数目(包括温度、压力和流量等)不少于440路,温度采集精度须达到±(2℃+0.5%×测量值),压力采集精度须达到±0.25%FS,流量采集精度须达到1%; 稳态参数采样频率须达到5~100Hz;动态参数采样频率须不低于200kHz。
2.5.2 试车台控制系统详细指标参数
2.5.2.1 电气系统
1) 电气系统用于给各工艺设备及控制设备供电,包括低压配电柜、电缆、桥架及桥架支撑等。电气系统的电气元件集成在电气控制柜内。
▲2) 电气系统须配有完善的熔断保护功能,留有将来设备增加或临时添加较大功率设备的余地。整个系统供配电为树状分级形式,各子系统对其设备进行配电,并确保三相用电平衡及功率因数符合国标规定。
2.5.2.3 控制系统
控制系统用于给试验设备供电,控制系统主要用于控制、反馈试验台各类状态参数,并通过调节试验件进口流量、进口温度、转速等参数实现工况的模拟。控制系统按照给定试验状态(如温度、试验件进口雷诺数、马赫数、流量等),自动调节进气调节阀组及管路系统阀组的开关量、冷却介质系统和润滑油系统供给参数、热空气压力温度流量参数、水系统的压力和流量,试验件转速与温度、压力能够按照设定规律联动运行。
1) 工位各系统阀门根据控制要求确定电动或气动驱动模式。
2) 为确保系统安全运行,控制系统还配置安全联锁、手动/自动以及急停等功能。各模块操作模式可分为手动控制和自动控制。
3) 当设备超载、超温、超转或试验件故障时,具备及时报警、防护和安全停车功能;同时有重要设备故障报警等,可直观、快捷的提示操作员准确做出判断。
4) 各系统的工艺流程图应在控制系统的显示器上予以显示,这些工艺流程图应显示测量和监测参数的数值变化情况及报警信息,这些参数以及报警信息能够被记录和回放。
▲5) 控制系统上位机须集成所有电气控制对象的操作控制输入,并在计算机屏幕上虚拟出与之对应的仪器、仪表、指示灯等。通过计算机屏幕就可完成对工艺设备、变频器等设备的操作、控制及动作指示,最大程度的取消操作台实物硬件,达到简化操作台设计的目的。
▲6) 控制系统设置上位机,采用软件编程,通过计算机操作界面,进行系统组态、监控和操作,实时监控温度、压力、流量等参数,并根据关键参数进行报警保护。
7) 控制系统须由CPU、PLC控制模块、控制柜、控制线缆、桥架等组成。
▲8) 控制系统应预留不少于10%的通道,控制柜设计应预留不少于20%的空间,以便将来增加新的PLC模块。
9) 系统应配置UPS电源,确保在断电情况下,系统仍能执行紧急关车、数据存储等相关操作,断电情况下运行不小于10分钟。
10) 控制系统软件要具有可靠性。
11) 要求在系统硬件选型时满足系统运算速度、控制精度、易维护性和可靠性的要求。
12) 系统应充分考虑安全运行等因素。
13) 操纵台用于满足试验人员对试验平台进行控制、数据采集和数据处理的需要。操纵台应满足多台位工作的操作需求。操纵台上应设置独立的紧急开关及指示器,紧急开关带有防止误操作保护。显示和操作终端为计算机,显示器应不小于27英寸。
2.5.2.4 传感器
各试验台位的设备用传感器主要为温度传感器和压力传感器。
① 温度传感器技术要求如下:
a) 传感器形式:固定螺栓式
b) 传感器分度:K型/T型/PT100
c) 精度:I级(用于性能计算)、II级(用于安全监测)
d) 电气接口:防水接线盒
② 压力传感器技术要求如下:
a) 精度:0.25%(用于性能计算)、1%(用于安全监测)
b) 工作温度范围:-30~80°C
c) 防护等级:IP65
d) 材质:不锈钢
2.5.2.5 数据采集系统
数据采集系统由气压扫描阀、稳态数据采集系统、动态数据采集系统和数采软件等组成。
1) 气压扫描阀
气压扫描阀用于测量试验件的气态介质压力,需满足的技术指标如下:
★① 采集通道数量:不少于140;
② 综合精度:±0.2% F.S.;
③ 响应:≯1ms;
④ 分辨率:16位;
⑤ 最大采样频率:每通道18kS/s;
⑥ 数据总线:以太网;
⑦ 工作温度:不低于-25~75℃。
2) 稳态数据采集系统
① 稳态热电偶采集仪用于试验件温度采集,热电偶信号可直接输入至热电偶采集仪,无需变送;若试验件传感器输出电信号,则需变送为标准信号输入至采集仪,技术要求如下:
a) 采集通道数量:不少于140
b) 每通道可单独配置热电偶类型,如J、K、T、E、R、S、B、N等
c) 输入通道16路差分模拟输入
d) 测量精度:±0.1%
e) 工作温度:不低于-25℃~75℃
f) 供电电源:18~36VDC
g) 通讯接口:以太网
② 稳态电压通用采集仪用于试验件电压信号采集,标准电压信号可直接输入至采集仪,无需变送;若试验件传感器输出电信号,则需变送为标准电压信号输入至采集仪,技术要求如下:
▲a)采集通道数量:不少于125
b) 电压信号:支持多量程输入
c) 单通道采样率:5000Sa/s
d) 测量精度:±0.1%
e) 工作温度:不低于-25℃~75℃
f) 供电电源:18~36VDC
g) 通讯接口:以太网
3) 动态数据采集系统
动态数据采集系统用于测量试验件的动态参数,包括瞬态温度、脉动压力、振动等,需满足的技术指标如下:
★①通道数量:不少于32通用通道+不少于3转速通道
②最高采集频率:不低于200kHz
③分辨率:不低于24bit
④各通道能够实现同步采样
4) 数采软件
用于对数据采集系统硬件通道进行定制化配置和对数据采集系统硬件通道传输出的信号进行工程化处理、显示、存储、后处理等,包括稳态数采软件和动态数采软件,需满足的技术指标如下:
① 稳态数采软件
稳态数采软件应至少包括数据采集软件、数据管理软件、数据处理/分析软件、实时监视软件、数据交换软件等模块,技术要求如下:
a) 系统应采用不低于Windows 10的操作系统。
b) 系统应包含一套关系数据库。该数据库将作为中央数据库,存储试验参数配置、试验信息、试验状态数据、性能计算数据、实时采集回放数据等。
c) 试验过程中录取的试验状态数据和性能计算数据必须即时写入数据库(结构化数据存储),实时采集回放数据可试验后导入(非结构化数据存储)。
d) 系统具有Web检索数据库数据能力。
e) 系统应提供友好的用户界面,便于向远程存储器存储和检索数据;系统在运行以下模块时应采用易于用户使用的图形界面:通道配置、自动化试验流程配置、校准、日志读写、数据后处理。
f) 态数据采集系统在线显示功能应配置为使用商业图形编辑软件包,使得用户(在对应的安全权限之下)能够自行创建、修改显示页面。除了在硬盘存储空间的限制外,显示页面可创建的数目不应存在限制,且应能在试验过程中实时编辑。页面修改应采用点击 — 拖拽控件的方式,修改后即时可用。
g) 显示刷新频率应可调,最高频率不低于1Hz。
h) 显示页面应能配置在任一显示器上显示。稳态数据采集系统应能允许任意时刻的即时截屏,且保存下来的信息存储或打印都应在后台进行,不得干扰显示刷新。
i) 稳态扫描功能,数据在用户指定的长度内进行平均的通道扫描;稳态数据扫描可以由试验程序自动(时钟)或报警动作触发,同时也必须提供手动触发的能力,用户初始化扫描通道时,系统应提供手动添加注释和从预定义注释表中选择合适注释的功能;稳态扫描触发与结束都应写入事件日志之中;试验状态数据和性能计算数据应不经中转程序即时直接写入数据库,且能供网络远程客户即时查看与分析。
② 动态数采软件
动态数采软件技术要求如下:
a) 可对同一个输入数据进行多种分析;
b) 能够实现时域信号分析、频域信号分析、时频分析、模态分析等功能,具体包括:数字滤波 、FFT 、功率谱(功率谱密度)分析、频响函数分析、实倒谱、复倒谱、逆复倒谱分析、自相关、互相关分析、概率密度、概率分布计算、阶次分析、小波分析等。
5) 其他指标
▲① 试验件引线下游的电缆、引压管、配套电缆桥架及附件、转接柜、数据采集设备、数采软件由投标人负责,投标人确保试验件数据采集系统的完整、可靠,以及布局的整齐有序。投标人提供的测试设备须同时提供厂家出具的相关证明文件,包括但不限于合格证、厂家测试报告等。
② 除了具有以上基本的技术指标外,系统还具有以下指标:
a) 可靠性、稳定性:传感器和数据采集系统具备高可靠性、稳定性;
b) 抗干扰能力:稳态采集系统和动态采集系统均需稳定可靠,并具有良好抗噪性能;
c) 集成度要求:稳态采集设备均要求高集成度,小体积;
d) 软件功能:稳态系统的采集软件界面友好,能够以多种方式实时显示测量参数值,试验后能以曲线图的方式对数据进行分析,动态系统的后处理软件能够实现对振动等信号的基础分析功能。
2.5.2.6 音视频系统
音视频系统包括视频监控系统和音频系统,主要用于完成对试验台场区和各能源站的主要监控点和重要通道等防护区域进行全面灵活的实时监视。视频监控系统由数字视频录像机、摄像机、显示器等组成;音频系统由话筒、音响、拾音器等组成。
1) 摄像头:16台(防爆功能不少于4台);
2) 显示屏:2块(55寸);
3) 音视频存储容量不应小于2T;
4) 可以调节每一台摄像机视频记录的帧频和图像分辨率;
5) 远程传输距离不小于300m。
2.6 后处理系统
2.6.1 后处理系统总体技术指标参数
★ 主流流量:5kg/s;分离油滴粒径:≥5μm;排气消音器出口噪音:≯70dB;后处理后温度:≯500K。
2.6.2 后处理系统详细技术指标参数
2.6.2.1 尾气除油装置
▲1) 在进行火焰筒油雾场试验和喷嘴热防护试验时,主流排气中含大量煤油蒸气和液滴,需经油气分离处理后,再经消音器排入大气。
2) 油气分离装置要求如下:
a) 粒径大于5μm的液滴要求综合分离效率达到99%;
b) 体积较小,结构简单,能够满足安装要求;
c) 由于气体中有夹带的液滴含有一定量的颗粒物和油分,在长期的工作中会在分离器表面形成结垢,所以分离器选择上应选择不易结垢的分离模式。
2.6.2.2 消音器
1) 消音器入口参数
排气流量:10kg/s(最大工况,包括排气、喷水);排气总压:0.11MPa; 排气总温:550K左右;噪声总声压级:130dB(A); 排气噪声频谱:双驮峰全频带。
2) 消音器出口参数
气流总压:0.104MPa;噪声总声压级:≯70dBA(消音器出口正中间上方1m处)。
2.7 排放测试系统
2.7.1 排放测试系统总体技术指标参数
★ 分析单元包含CO、CO2、UHC、NO、NO2、H2O、O2组分,设备测量精度1%。
2.7.2 排放测试系统详细技术指标参数
燃气分析系统由气体分析仪、取样耙、取样选择器、预处理系统、采集与控制系统及其配套水、电、线缆、桥架构成。
2.7.2.1 主要指标要求
★1) 燃气分析系统用于燃烧效率测量和燃烧尾气成分分析,需要包含CO、CO2、H2O、NO/NO2、UHC和O2等分析仪;
★2) 燃气分析系统数据须与燃烧试验台排放测量系统稳定通讯;
★3) 燃气分析系统数据须与半物理仿真试验台示踪气体浓度测量装置稳定通讯;
4) 气体成分测量精度优于1%;
5) 湿度测量:精度优于±0.4℃(冷凝露点湿度计)或优于读数的±5%(电容式湿度计);
6) 单点采样传输不大于10 秒;
7) 系统响应(含气体成分响应
和样气的传输
)≯ 20 s(复合电伴热保温管按长度20 m计算);
▲8) 满足《HB 6117-2020航空燃气涡轮发动机气态污染物的连续取样及测量方法》要求。
2.7.2.2 软件技术要求
▲1) 能实现快速自动采样,在线测量多种成分的浓度(包括CO、CO2、NOx、O2、H2O、UHC等多种气体),通过集成相应程序可实时计算出燃烧效率和余气系数等性能参数,易于操作使用。
2) 能通过网络实时与测试、控制系统通讯。
2.7.2.3 其他要求
1) 燃气分析系统设置独立的预处理控制、采集、分析功能,须配套提供软硬件,具备独立运行能力。
2) 燃气分析仪布置根据试验件空间布置合理位置,整体可移动。
3) 燃气分析系统桥架、电缆、供电采取合理的屏蔽和接地措施,避免外界信号干扰,其中取样管设置单独桥架。
▲4) 提供测试段引出样气装置,通过控制系统控制样气切换,样气进入取样选择器后进行样气预处理,经过预处理的样气进入燃气分析仪进行测量;定期对取样管路进行反吹,反吹气不允许进入燃气分析仪内。
5) 测量烟气成分、测量范围、测量精度等参数须满足下表。
表6 烟气分析仪详细指标参数
序号 | 数量 | 名称 | 技术参数 |
1 | 1 | CO/CO2/O2分析仪 | -测量原理:NDIR测CO/CO2,磁氧测O2-测量范围:CO 0~500/1000/5000ppm,C02 0 ~10/20%,O2 0~10%/25%多量程可选择和设置,量程自动切换;-测量精度:不大于±1%FS; |
2 | 1 | NO/NOx在线分析仪 | -测量原理:高温型化学发光法CID:-测量成分:NO、N02、NOx;-工作气体:零空气;-测量范围:0~3/30/300/3000ppm,多量程可选择和设置,量程自动切换;-测量精度,不大于±1%FS; |
3 | 1 | H C 在 线 分 析 仪 | -测量原理:火焰离子检测法FID-燃料气:氢气/氦气混合气;-助燃气:零空气;-测量范围:0~30/300/3000/30000ppmC,多量程可选择和设置,量程自动切换;-测量精度:不大于±1%FS; |
4 | 1 | 样气预处理系统 | 包括取样泵,高温过滤,调压,反吹,泄漏检查,冷凝,泄压保护、流量调节、伴热 、温控、压力温度控制等 |
5 | 1 | 温度场前级取样箱 | 包括5路进样,高温开关阀,泄放阀,调压,过压保护、伴热、温控、压力温度控制等 |
6 | 1 | 控制系统硬件 | PLC,上位机,交换机,电控等 |
7 | 1 | 标定单元 | 标气瓶、标定管路、切换阀等 |
9 | 1 | 系统控制软件 | |
10 | 1 | 安装及施工 | 现场调试及培训,且相关专业培训不少于1周 |
2.8 气源系统(含空压站、气罐和加热系统)
2.8.1 气源系统总体技术指标参数(含空压站、气罐、加热系统基底建设)
★1) 空压机数量2台,每台压缩机排量≮500 m3/h,最大工作压力≮26 MPa,含配套冷却、空气过滤处理装置。
★2) 气罐数量8台,单台气罐容积30 m3,最大工作压力≮26 MPa,罐体内表面须采用高强度、耐腐蚀金属材料。
▲3) 空压机须含有干燥冷凝器,且与气罐须高效匹配,完成全容量的充气不超过50小时。
★4) 1#电加热器最大空气流量5 kg/s,最大工作压力不低于3 MPa,最高工作温度850 K;2#电加热器最大空气流量1 kg/s,最大工作压力不低于3 MPa,最高工作温度500 K。
▲5) 两台电加热器的气压损失须均不超过0.15 MPa。
▲6) 加热系统须包含相应的电动调节阀、调功柜、开关柜等,且电加热速率可动态连续调节。
▲7) 气源系统的电加热能力须覆盖以下两表工况。
表7 气源加热能力检验工况-1#电加热器
空气流量 kg/s | 工作压力 MPa | 工作温度 K |
5.0 | 3.0 | 850 |
3.0 | 3.0 | 750 |
1.0 | 3.0 | 650 |
表8 气源加热能力检验工况-2#电加热器
空气流量 kg/s | 工作压力 MPa | 工作温度 K |
5.0 | 3.0 | 500 |
0.8 | 3.0 | 600 |
1.0 | 3.0 | 500 |
2.8.2 气源系统详细技术指标参数
2.8.2.1 概述
1) 气源系统由空压站、气罐组和大功率电加热器等组成。气罐总容积240m3,气源压力≮26MPa,管路上配置进气总阀等。
★2) 气罐至C座之间的高压气管路通径不小于DN65,压力≮26MPa,长度≮120米。
3) 空气加温器位于进气系统中,用于对常温空气进行加温,供往试验工位。
2.8.2.2 功能要求
1) 空压站功能要求
① 空气站主要由空气压缩机、干燥器、气路管路系统(背压阀、止回阀、管道等)、冷却水系统及设备配电系统。
② 干燥净化系统主要由中间级冷干机、压缩空气出口干燥器、前置除油初级过滤器、前置除油精密过滤器、后置除尘过滤器等组成。
③ 考虑系统的功能性、实用性、灵活性,以及整套系统的集成度与适用性,压缩空气系统、空压机冷却水系统及分离排污系统公用一套控制系统,并能实现远程通讯。
④ 机组安装在同一底架上,整体设计结构紧凑、体积小、重量轻。
⑤ 在建设完成基底后,须对现有建筑场地地面和周围结构进行核算,确保基底能够承受设备所产生的载荷。
2) 气罐组功能要求
① 气罐为卧式布置,要求气罐之间留有合适间距,便于检修。
② 气罐底端留有排污口。
③ 在建设完成基底后,须对现有建筑场地地面和周围结构进行核算,确保基底能够承受设备所产生的载荷。
3) 大功率电加热器功能要求
① 电加热器可在较宽的空气压力和流量范围内正常工作;
② 电加热器加温速率可调;
③ 电加热器出口温度可调;
④ 电加热器可通过试验器电气控制系统进行远程控制;
⑤ 电加热器出现超温、超压和通过流量小于流量下限等异常现象时可报警提示和自动保护;
⑥ 电加热器节能高效,工作稳定可靠;
⑦ 加温器的位置设计应离试验件尽可能近,尽量减小其出口管道的热惯性;
⑧ 流经两台电加热器的气流压力损失须均不超过0.15MPa。
2.8.2.3 技术指标
1) 空压站技术指标
▲ 数量:2套;排气压力:≮26 MPa;单台空压机排量(标准状态下):≮500 m3/h;输气温度:≤45 ℃;含油量:≤1 mg/m3;尘埃粒子:≤1 μm;露点: ≤ -55 ℃;温度: -15 °C~+45 °C, 连续运转;相对湿度 0~100 %(标准大气压环境温度20 ℃);
2) 气罐组技术指标
▲ 单罐尺寸:容积30 m3;工作压力:≮26 MPa;腐蚀裕量:3 mm;工作温度:-19 ℃~60 ℃;工作介质:空气;罐体材质:16MnR(参考);安装形式:卧式;数量:8台;需要对现有建筑场地地面和周围结构进行核算,确保基础能够承受设备所产生的载荷。
3) 大功率电加热器技术指标(大流量)
★ 电加热器最大进口压力:≮3MPa;电加热器进口流量范围:0.5~5kg/s;电加热器最高出口温度:850K;电加热器出口温度控制精度:≤±2K;电加热器升温速度:满足进气系统升温速率要求(≮20K/min);电加热器加热效率:≮85%。
4) 大功率电加热器技术指标(小流量)
★ 电加热器最大进口压力:≮3MPa;电加热器进口流量范围:0.1~1kg/s;电加热器最高出口温度:500K;电加热器出口温度控制精度:≤±2K;电加热器升温速度:满足进气系统升温速率要求(≮20K/min);电加热器加热效率:≮85%。
2.9 天然气系统
2.9.1 天然气系统总体技术指标参数
★ 供给背压:3MPa;天然气流量调节范围:10~100 g/s,须兼容H2、NH3和CO等气体,且每批次纯度不低于99.99%。
2.9.2 天然气系统详细技术指标参数
2.9.2.1 功能要求
▲1) 系统应具备可靠的远程和现场手动切断功能,能在发生意外而需紧急停止介质供给时,可在3秒的内将气体燃料供给快速完全切断;
★2) 系统工作过程中不允许有气体燃料泄漏;
★3) 可灵活、便捷地对燃料的流量在招标人要求的范围内进行连续调节;
★4) 系统应具备超压泄压及反压过高时止回的功能;
★5) 为保障系统运行安全,供给管路末端应设置阻火器;
▲6) 氮气吹除压力应高于喷嘴反压,确保不会出现燃料倒流现象;
▲7) 氮气吹除系统压力可根据不同试验工况的需要进行调节。
★8) 须兼容H2、NH3和CO等气体。
2.9.2.2 指标要求
▲1) 天然气燃料系统主要用于为试验件提供满足工况要求的天然气等燃料,兼有为半物理仿真物理试验台二次流路提供示踪气体功能,系统包含天然气储存系统、流量调节输送系统、CO2示踪气体输送系统和氮气工艺气系统等。
2) 技术指标如下:
① 供给背压:≮3.0MPa;
② 天然气流量调节范围:10 g/s-100 g/s。
③ 实验≮1200s。
2.10 附件
2.10.1 光纤耦合探头装置
1)耦合调节器:激光波长532nm和561nm。数量不低于4个;
2)探头耦合器:中继激光波长532nm和561nm;
3)探头前置透镜:直径112mm 焦距500mm 可消色差;
4)二维探头:孔径60mm 光束直径2.2mm 光纤长度5m。
2.10.2 磁力耦合式振荡发生器
1)220V供电,额定压力不小于5MPa,高压齿轮流量计,耐压不低于10MPa;
2)振荡检测传感器耐压不低于10MPa,并配套信号传输至控制柜PLC;
3)储油箱为不锈钢材质,有效容积不低于100L,装置控制柜为220V供电,调节流量的振荡频率和振幅,并配套DN14~DN18的高压电动球阀、减压阀、调压阀、高压过滤器和管路,包含调试费和运输费;
4)燃油振荡频率0~800Hz,振荡幅值5%~10%;
5)技术服务和售后服务长期有效,配件免费更换。
2.10.3系统控制主机1
1)架式控制主机,产品尺寸长不小于720mm;宽不小于440mm;高不小于45mm;
2)系统为windows Server;
3)核数不小于256,线程数不小于512,CPU颗数至少2颗,主频不小于3.1GHZ ;
4)内存不小于256G;
5)固态硬盘不小于3*4TB;
6)电源为白金级双热拔插,功率不低于1400 W的冗余电源;
7)网卡:前端口:1个VGA,1个USB 2.0接口,1个专用IDRAC Direct Micro-USB接口。后接口:1个VGA,1个USB 2.0接口,1个USB 3.0接口,2个RJ45;
8)前端口:1个VGA,1个USB 2.0接口,1个专用IDRAC Direct Micro-USB接口.后接口:1个VGA,1个USB 2.0接口,1个USB 3.0接口,2个RJ45;
9)包含导轨,滑道显示屏,鼠标键盘等附件。
2.10.4 系统控制主机2
该系统控制主机须提供2台。
表9 系统控制主机详细指标参数
控制主机 | 数量 | |
CPU | AMD EPYC 9654 96C 360W 2.4GHz 处理器 | 2 |
内存 | 32GB TruDDR5 4800MHz(2Rx8)RDIMM | 12 |
硬盘1 | 480GB 读密集型 SATA 6Gb 热插拔固态硬盘 | 2 |
硬盘2 | 960GB 读密集型 SATA 6Gb 热插拔固态硬盘 | 3 |
硬盘3 | 8TB 7.2K SATA 6Gb 热插拔 512e 硬盘 | 2 |
SAS RAID | RAID 9350-8i 2GB 闪存 PCIe 12Gb 适配器 | 1 |
GPU | NVIDIA RTX A2000 12GB PCIe 主动式 GPU | 1 |
网络1 | Broadcom 5719 1GbE RJ45 4 端口 OCP 以太网适配器 | 1 |
网络2 | Broadcom 57414 10/25GbE SFP28 2 端口 PCIe 以太网适配器(含万兆光模块) | 2 |
电源 | 1200W(220V 交流/240V 直流)热插拔电源模块(1.8 米电源线1根) | 2 |
附件 | 导轨 | 1 |
三、试验平台安全指标要求
3.1 试验平台材料安全指标
3.1.1 管路材质
试验平台的管路组件(如管道、管件、阀门、流量计等)材质最低要求为304不锈钢。
3.1.2 管路支架
管路支架宜采用普通碳素钢。
3.1.3 管路保温材料
1) 对于高温管路,管路保温材料应具备质轻、易加工、不易破碎、容易检修和维护等特点;
★2) 管路保温材料应不产生粉尘,对人体无危害;
★3) 室内管路保温材料在火灾时,应不产生有害气体或大量烟气。
3.1.4 外观及标识
1)设备应无目视可见的锈蚀、裂纹、孔洞、变形、残损;
2)酸洗:不锈钢管道焊接完成后焊缝应进行酸洗,形成钝化保护膜,清除表面污渍和变色,使其外观干净整洁;
★3)设备标识:
a) 燃气管路、高压气流管路、高温管路等需要有颜色标识,包括井盖等;
b) 试验台中的流体介质管路(如空气、燃油及冷却水等)应按招标人认可的相关标准采用颜色、箭头和符号等措施做出明显标识,防止混淆和误操作;
c) 各类安全标识配置齐全;
d) 配置试验前检查单,对于螺栓紧固等内容进行标识,明确试验前安全检查项。
3.2 试验平台质量安全性及维护要求
3.2.1 操作性要求
1)试验台的操作/控制模式:试验台可采用就地和远程两种操作/控制模式;
2)试验台的操作/控制所需人员数量:不超过3人,其中2人负责试验台状态调节,1人负责数据采集。
3.2.2 可维护性
1) 需要更换的部件采用插入式连接结构、螺纹连接结构或法兰连接结构;
2) 除试验台控制系统外,其它系统硬件设施维修技能人员不低于高级工水平;
3) 电气控制软硬件系统的维修更换人员不低于专业助理工程师水平;
4) 高空、靠墙等需要维护维修的部位,有可达通道、足够的维修空间、人员安全防护设施。
5) 试验平台的试验台控制系统应预留一定接口,供未来升级及功能扩展,传感器方便检查拆卸。
3.2.3 完整性
1) 交付产品的性能符合技术要求的规定;
2) 产品结构设计,包括可靠性,维修性和寿命等,符合技术要求及强制性国家标准、行业标准的规定;
3) 产品的制造、组装、检验及调试符合设计要求。
3.2.4 可移植性
试验平台测控软件应具备较好的兼容性,在更改运行环境、计算机操作系统升级或更换计算机硬件后,不必经过大幅修改即可实现原有功能。
3.2.5 安全性
1) 防护等级:试验平台电气设备防护等级为IP54;
★2) 特种设备:高压气罐等特种设备以及压力管道等,需提供厂家资质证明等;天然气存储系统等涉及安全性,需提供容器制造资质等;
3) 机械:试验平台应有防挤压、剪切、缠绕、吸入/卷入、冲击、刺伤/扎伤、摩擦/磨损、流体喷射、滑倒/倾倒/跌落功能;
4)所有管道密封应安全可靠,不允许漏水、漏油、漏气;
5)空气管道的热应力应采取可靠措施予以消除;
★6) 电气:试验台控制系统应具备有防漏电、触电、静电、过流、过压、欠流、欠压、过载、短路等报警功能;
7) 对于电气控制系统,应制定两级报警,自动有效规避事故发生;
★8) 温度:试验台的空气管道应按相关规范采取安全、可靠的隔热措施,确保不会对人员和环境造成危害;所有排气管道进气温度如超过300℃,应采取可靠的降温措施将排气温度降至300℃以内;试验过程中试验间应采取通风措施使室内的环境温度保持在40℃以下的范围内,确保测试仪器仪表的正常工作。
★9) 材料:试验平台选用的材料应无毒、无害,不会造成环境污染。
10)振动:所有设备管道的支撑牢固可靠,工作时无明显振动。
3.2.6 设备后期处理
试验平台达到寿命报废后,应满足以下处理要求:
1) 所有金属材料的零部件应均可回收;
2) 设备应便于分解、拆卸和运输,不能在试验厂房内残留不可拆解的废弃物;
3) 试验区域所有拆解物质量均不应大于所配天车的最大起重量。
3.2.7 消防安全及其它
1)试验台厂房布局布局应充分考虑人员的操作和安全,发生火灾时试验间应有紧急出口,消防安全通道等必须设置合理。
2)试验台整个系统自身应具有故障诊断和报警功能,设有应急按钮。在设备出现超压、超温等意外情况下可自动报警,手动应急停车;
3)试验器整个系统应具备异常停电、停气、停油和停水条件下的自保护功能;
4)具备安全保护设计措施,确保人员、设备和数据的安全。
商务要求:
★1、交货:合同签订后2年
★2、交货地点:沈阳航空航天大学指定地点
★3、付款方式及条件:合同签订后3日内中标人提供合同金额70%的预付款保函(预付款保函为见索即付保函;保函开具前,必须将保函文本向甲方申报,并经甲方确认保函所有条款后,再行开具正式保函;索赔不得附加需中标人同意或需中标人提供证明材料条款,保函有效期不低于24个月),采购人收到预付款保函后,支付70%的预付合同款;待项目建设12个月时,经过专家审核评估后,有阶段性成果,论证通过后,中标人提供合同金额30%的预付款保函(预付款保函为见索即付保函;保函开具前,必须将保函文本向甲方申报,并经甲方确认保函所有条款后,再行开具正式保函;索赔不得附加需中标人同意或需中标人提供证明材料条款,保函有效期不低于12个月),支付剩余30%合同款。
★4、质量保证期:2年,计算从项目完成并经验收合格后开始计算。质量保证期内中标人不收取任何维修费用,质保期后中标人对易损件收费低于市场价且合理,不收取人工费。
★5、热线支持:提供
现场支持:2小时内响应;48小时内到达
★6、特殊要求:以人民币为结算单位,本项目报价包含履行本合同至项目交付有关的一切费用,采购人不再单独支付其他任何费用。
★7、验收标准:按照国家及行业相关验收标准进行验收
验收程序:按照辽财采【2017】603号《辽宁省政府采购履约验收管理办法》规定执行
验收报告:按采购方验收报告填写
组织验收主体:本项目的履约验收工作由招标人依法组织实施。
★8、其他要求:
(1)项目建设期内项目负责人全程驻场,未经采购人允许不得更换项目负责人。
(2)本项目为成品交付项目,项目验收合格后,需通过实际运行测试后方可交付。
合同履行期限:合同签订后2年
需落实的政府采购政策内容:1.对于中小微企业(含监狱企业)的相关规定;2.对于促进残疾人就业政府采购政策的相关规定等。
本项目(是/否)接受联合体投标:否
二、供应商的资格要求
1.满足《中华人民共和国政府采购法》第二十二条规定。
2.落实政府采购政策需满足的资格要求:无
3.本项目的特定资格要求:无
三、获取招标文件
:20
11月2
23时50分至20
12月0
00时00分(北京
,法定节假日除外)
本招标项目仅供正式会员查阅,您的权限不能浏览详细信息,请点击注册/登录,联系工作人员办理入网升级。
联系人:刘欣
电话:010-56240287
手机:13522553206(欢迎拨打手机/微信同号)
邮箱:kefu@bidnews.cn
- 款 付款指导
- 续 老会员下载续费申请表
- 新 新会员下载会员申请表
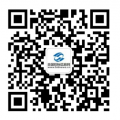
- 南京理工大学可见及近红外激光量子信息高精度调控测量系统竞争性磋商公告 2024-12-04
- 邢台章泰矿业有限公司2025年9T卡轨车、三环链、连接插销、提升机设备安全技术检测项目公告 2024-12-04
- 江西分公司南昌东站站房及相关工程项目附属用房室外工程专业分包招标公告 2024-12-04
- 2025年-2027年马桥镇大居道路保洁服务的招标公告 2024-12-04
- 西太湖国际露营岛(南区)项目土建工程招标公告 2024-12-04
- 山西铁路装备制造集团轨道交通有限公司职工食堂食材采购项目招标公告 2024-12-04
- 山西安泽农村商业银行股份有限公司宣传品、印刷品服务单位框架协议招标变更公告 2024-12-04
- 中国广电内蒙古网络有限公司额济纳旗分公司额济纳旗2024年民生实事项目农牧区电视宽带网络覆盖工程施工服务竞争性磋商公告 2024-12-04
- 山西洪洞农村商业银行股份有限公司保安劳务派遣服务项目招标公告通知 2024-12-04
- 中冶天工铝业公司500KA电解槽节能、技改项目劳务分包工程招标公告 2024-12-04